DTP Tablet Press Range
Fill out your details and our team will provide you with a full quote as soon as possible.
- 3,600 tablets per hour
- Up to 25 mm
- 50 kN max. pressure
The DTP series consists of two advanced tablet presses that incorporate many refinements to make tablet pressing faster, easier, more efficient and safer. The DTP 12 and DTP 25 are both single head, continuous operation pill presses that offer high efficiency in the use of raw materials and easy operation through an electronic control panel.
Get information on the DTP Tablet Press Range
The DTP tablet presses benefit from the simple adjustment of all key parameters, low noise, and safe operation. They are compact machines that are light in weight for their class yet apply a hefty 50 kN of pressure to produce top quality, pharmaceutical grade tablets that are highly consistent in weight. Thanks to their feeder mechanisms, these tablet presses are extremely efficient in their use of raw materials.
Both the DTP 12 and DTP 25 are modeled on the same format, each capable of producing 3,600 per hour, with a maximum diameter of 12 mm on the DTP 12, and 25 mm on the DTP 25.
Designed for pressing dry powders and granular material into tablets, these tablet pressing machines are widely used in the pharmaceutical, chemical, electronic, foodstuff and other industries, and represent a cost effective solution for any application that requires moderate quantities of high quality tablets.
Main benefits at a glance:
- Clear turret shield to meet GMP requirements for enhanced operator safety and preventing cross-contamination of powder between batches
- Achieves high raw material efficiency
- Simple-to-use electronic control panel for minimal operator training
- Highly standardised output thanks to advanced feeder mechanism
- 50 kN pressure for strong, properly finished pharmaceutical grade tablets
- Safety cut-out button for emergencies
- Quality design and construction for reliability and ease of maintenance
- Outstandingly engineered transmission maintains stability
- Low-noise operation for improved operator comfort
- Four-pillar structure provides larger operation area
- Portable machines, low weight for their class
Features
These tablet presses are both aimed at users who want convenience and ease of use rather than large scale commercial mass production. As such they have been enhanced with all the modern features that make pressing tablets simple and efficient. A clear turret shield protects the operator from risk of harm when the machine is running, while also preventing powder flying around the room and causing cross contamination. Combined with an efficient feeder mechanism, this gets the most productivity out of expensive raw materials. And an easy-to-follow electronic control panel makes it quick and easy to understand the machine’s status and to adjust key parameters such as production speed.
These machines weigh just 100 kg and 150 kg respectively, making them far lighter than any large industrial tablet presses, and are small enough to be reasonably portable. Despite their comparatively low weight, the DTP machines are able to achieve an impressive 50 kN of pressure to produce top quality tablets up to either 12 mm or 25 mm diameter, making them suitable for most popular tabletting applications. They both have a maximum production speed of 3,600 tablets an hour, making them ideal for hospital or research facility use, as well as commercial production that requires moderate volumes.
The refinements on these machines go more than skin deep, as the DTP tablet presses feature stable, solid transmissions and engineering to give reliability as well as performance and ease of use.
DTP Series Tablet Presses in Use
The key stand-out points for the DTP Series tablet presses are ease of use and quality of the design. Operator comfort and safety have been enhanced by the inclusion of several important features. A safety cut-out button allows a quick shutdown to cope with any emergency that arises, and the low noise operation that comes from an outstandingly engineered transmission mechanism makes the machine’s environment much more pleasant. The ability to produce useful quantities of tablets on a machine that does not require a crane to lift it from location to location, also counts as another plus point. Laboratories or hospitals will find this portability a significant advantage as it allows the machine to be relocated between departments when required.
Ultimately a tablet press is judged by its output. Small, light-weight machines sometimes struggle to achieve the pressure needed for commercial grade tablets, but with 50 kN of pressure for each model, the DTP series presses have all the pressure you could ask for. As a result they produce dense, properly compacted tablets that easily meet and exceed the requirement for pharmaceutical production.
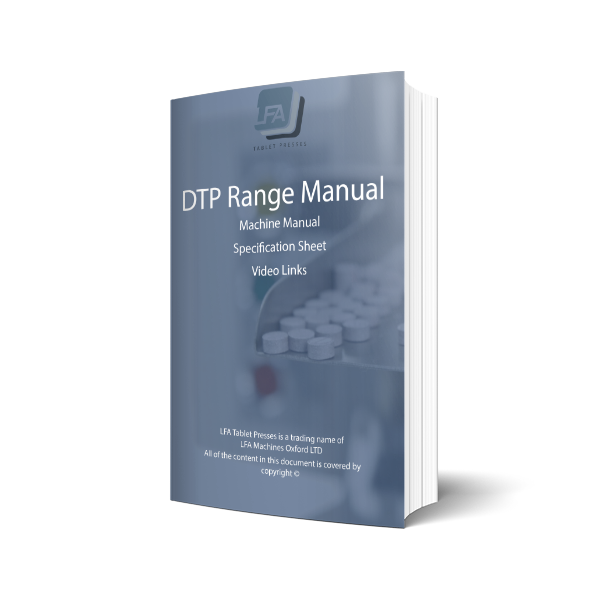
Get Information on
DTP Tablet Press Range
Enter your details to get the User manual, Spec Sheet and Video links for DTP Tablet Press Range
Our View
Both of the machines in the DTP series are excellent choices for a laboratory or small production facility, where high quality tablets are essential but the maximum of 3,600 tablets per hour is sufficient to meet demand.
The main difference between the two machines is the maximum diameter of tablets produced. For the DTP 12, a maximum diameter of 12 mm covers the most popular sizes of commonly taken tablet, but may not be sufficient for some herbal or mineral supplements that require greater volume. For situations where a larger tablet might be needed, the DTP 25 is ideal.
Weighing in at just 100 kg, the DTP 12 is particularly portable, which may be another factor to consider. Even with its 150 kg weight, the DTP 25 is far lighter than our large, industrial sized machines, and is capable of producing up to 3,600 tablets per hour.
With their ease of use, safety features, raw material efficiency and advanced engineering, both the DTP 12 and the DTP 25 are outstanding choices within their class.
The LCD touch screen is an important innovation that makes life so much easier, because it greatly simplifies the machines’ operation. Manually adjusting everything is always a time consuming chore, so having important functions adjusted on screen is a definite benefit.
Over all, if you need to produce a large volume of tablets, these are the fastest and most dependable presses to do this. They pay for themselves very quickly thanks to reduced unit and human operator costs.
Technical Specifications
Model | DTP25 | DTP12 |
---|---|---|
Dies (sets) | 1 | 1 |
Maximum Dia. of Tablet (mm) | 25 mm | 12 mm |
Max pressure (kN) | 50 | 50 |
Max depth of fill (mm) | 20 mm | 20 mm |
Tablet thickness (mm) | 8 mm | 8 mm |
Motor Power (kW) | 220 V/50 Hz, 1.5 kW | 220 V/50 Hz, 1.1 kW |
Overall size (mm) |
580 mm×500 mm×830 mm |
550 mm×450 mm×750 mm |
Weight (kg / lbs) | 226 kg / 498.3 lbs | 100 kg / 220 lbs |
Max tablets p/hour | 3,600 | 3,600 |
Yes, this could be down to corrosion or due to oxidation of your product. We would highly recommend taking your tooling out of the press and cleaning it at the end of every production run.
We would also recommend polishing the tooling to keep the surfaces clean and less likely to cause picking or capping.
Probably not, unless you have a very big autoclave. You can, however, put all of the contact parts in one. The boot, tooling and hopper are all detachable and can withstand 120°c in an autoclave of 20-30 mins.
Yes, this feature is built into all of the new DTP 25 presses.
In the old DTP 25 presses, this feature is not standard. However, they can be fitted very easily.
The first time you change a set of tooling on the DTP 25 it can take about 30-40 mins. With practice, this can easily be got down to under 10 mins.
No. The DTP 25 does not come with any tools included in the cost of the press. However, most of the tools used on the press are very standard. The only tool that would not be considered standard would be a Die Insertion Ring and Die Seat Cleaner.
A link to these items can be found here: Die Seat Cleaner & Insertion Ring
That will depend on the use of the press and the part you are greasing. We have completed a full lubrication schedule to help you understand what parts need lubrication when. The lubrication schedule can be found here:
Yes, in the event that your perspex becomes broken we are able to supply a new set for you. We stock and offer several spare parts for the DTP 25.
They can all be found here:
Yes, on version 2 of the DTP 25 there is a threaded hole in the top of the press just off of the centre that is designed to take an M16 threaded bolt with an eyelet. This part comes included with the press. To lift the DTP 25 insert the eyelet in the threaded hole and then use mechanical lifting to hoist the press.
On older versions of the DTP 25 there is not always a threaded bolt in the top of the press. If yours is one like this then we recommend using two lifting straps to hoist the press. Run the first strap behind the central separating perspex sheet next to the motor. Run the second lifting strap in front of the upper drift pin assembly but behind the structural supporting bar. Connect the four ends of the two straps in a single point in the centre of the press above the main cover. Make sure to protect any edges with something soft like cardboard or fabric.
The machine runs at 80 dB, when at full speed.
We recommend ear protection for a long exposure as repeated noise can cause hearing damage.
Yes, despite the fact that they are a DTP press, we have made sure that they take the TDP Universal Tooling. This makes it easier to ensure that you are able to get the correct size tooling every time.
Yes, the press does have a variable speed control. It can be run between 10-50 RPM.
This speed control is varied using a variable adjuster and the speed is shown on an LCD readout.
Note: It technically can be run slower than 10 RPM but the press is likely to not have the kinetic motion to complete the compression of a tablet.
Yes, the machine does come fully assembled. The feet are attached during shipping. We support the press with 4 additional strips of wood.
The hopper capacity of the DTP 25 is approximately 3l. Depending on the bulk density of your powders, this will hold around 3-5 kg. It is, however, important to remember that the press should not be left unattended during production and that an operator should be with the machine at all times.
The cleaning downtime of the DTP 25 will depend on how thorough you want to be. We recommend cleaning your machine in one of two ways:
1. If you are going to be continuing production from one product to another with the same tooling and no cross contamination issues, then we recommend a light clean. Here are the steps:
Remove all remaining powder from the press.
Remove hopper.
Hoover up excess powder from the inside of the press making sure to get inside the boot and around the base of the press.
Reassemble the press.
2. At the end of every day/run and if there is a potential for cross contamination, then we recommend the following procedure:
Remove all remaining powder from the press.
Remove hopper, boot and tooling.
Hoover up excess powder from the inside of the press.
Wash parts with warm soapy water.
Rinse the parts with potable water.
Sanitise the parts using a sanitising solution.
Dry the parts to reduce the chance of rust.
Lubricate the parts if specified in the lubrication schedule.
More information about cleaning the DTP series can be found here:
Yes, on version 2 models of the DTP 25 there is a jog button. It is the yellow button in between the red and the green button.
On some of the older versions of the DTP 25, there are not any door alarms or sensors. However, it is possible to retroactively fit them.
On newer models, there are door sensors that shut off the machine if the doors are opened.
Other than the maximum tablet size, there is not a massive difference between the DTP 12 and DTP 25. The DTP 12 has a smaller motor as it requires less power, making it lighter and smaller than the DTP 25.
A detailed comparison of the DTP series specifications can be found here:DTP Technical Specifications
The handle to operate the machine manually on the DTP 12 or 25 is currently located on the bottom of the motor.
The DTP comes with an emergency punch stop button as specified on the website.
The control panel on the top controls the stop, start, and jog functions as well as the speed of the press.
The pressure of the DTP is adjusted on the top of the Upper Drift Pin Assembly and the fill depth is adjusted with the lower drift pin assembly.
Yes, it can. The speed of the press is controlled using the speed adjustment on the control panel that is located at the top of the press.
Yes, the press can be used for production purposes. If you are having to run the DTP press for 8 hours a day 5 days a week, then we suggest upgrading to a rotary press. Not only would it save you time because it’s easier to use, but the cost is not much higher. The RTP 9 Rotary Press would be a good machine to look at if you are new to rotary presses.
Yes, you can order any set of tooling you like for the DTP and we will install it in the press before it is sent out to you. Additional tooling can be found here: TDP Tooling | Punch & Dies for TDP Pill Presses
If you would like custom tooling, then you will need to fill out a custom tooling order form and contact the sales team with the reference number that can be paired with your machine. The turnaround time for custom tooling is about 6-8 weeks. Our custom tooling order form can be found here: Custom Tooling
Yes, it is possible to make shaped tablets on a DTP machine. The pressure is adjusted in a rotational motion, so it is more tedious to use shaped tooling since you have to adjust the top punch position every time you adjust the pressure.
Yes, the maximum size for shaped and round tablets on the DTP 12 and 25 are the same as round shaped tablets.
The DTP is easier to clean as the powders are not able to get onto the motor, electronics, gearbox and other component parts.
Another big advantage is that it complies with GMP regulations.
The DTP is, however, heavier, slower, and more expensive so it really depends on your needs.
None, it gives a readout of the speed at which the press is running.
No, it does not have a PLC. The Variable Frequency Drive that runs the main motor does have a network cable that allows you to integrate it into a larger system, but this is not something that LFA supports.
Yes, there is a manual weight adjustment to help you control the fill depth of the lower punch. This allows you to control the weight of your tablets.
No, we do not offer mini hoppers. You do not have to completely fill the powder hopper when using the press. We are able to supply you with additional hoppers if you would like to be able to have a quick turnover between production runs.
Honestly, not a lot. Aesthetically speaking, the DTP would look nicer, but the TDP 6s in a cage or a perspex box will perform to a very similar standard. The only difference would be the speed adjustment which the TDP 6s does not have. The ability to adjust the speed on the DTP allows you to adjust the dwell time.
The fact that the DTP will not run without the doors being closed means that the operator is unable to get access to any moving parts. With the TDP 5 and the TDP 6s, there are exposed moving parts that the operator has to be aware of.
The DTP is not really any easier to use than the TDP range. The way that you adjust the punch pressure and fill depth is very similar.
You can run the DTP 25 with 50g of your mix. The thing that you need to be aware of is that the lower you go with the amount of powder in the hopper, the less consistent the tablets will be. You can combat this by running the press slower but this will also increase the dwell time.
We would recommend the DTP 12/25 over an RTP 9 if you needed to do very small runs of tablets for testing or in a compounding pharmacy. The time it takes to clean and change the tooling on the DTP Tablet Presses is a lot shorter than the RTP 9’s. On the other hand, if you need to produce larger batches of tablets, then you should go with the RTP 9.
On the DTP there are no cast parts. The majority of the contact parts are either made from aluminium, stainless steel, or Teflon.
The capacities for the hoppers on the DTP 25 and the DTP 12 are as follows:
DTP 12: 2 liters
DTP 25: 3 liters
This makes the hoppers on the DTP range much bigger than the hoppers on the TDP series.
This being said, we do not recommend under any circumstances leaving the machine unattended for long periods of time. An operator should always be present when running the machine.
Yes, we could fit the DTP 25 with 3 phase power, however, we would not recommend it. It would increase costs, due to the power consumption on the motor.
The DTP 12 and DTP 25 have 6. These will take a range of different grades and viscosities of grease depending on the application.
To help you with this we have created a lubrication schedule which can be found here: DTP 25 Lubrication Schedule
No. In 2017 LFA made the decision to standardise all desktop tablet presses to one size of tooling. This is called TDP Universal Standard Tooling. We have also adopted this size of tooling in our DTP range of presses.
The full details of this tooling size can be found here on our website: TDP Tooling
The machine requires constant supervision. It is unlikely that the press will jam once it has been calibrated and in the event that it does there is a pressure overload mechanism to shut off the machine. However, this does not mean that the machine should run on its own. If the machine jams, it is critical that the operator is present to apply the emergency stop button as soon as possible.
No. We recommend that you find a bench, desk, or base that can hold the press at a comfortable height for the operator to work at (60-90cm).
It is also important that the bench is able to support the weight of the machine and additional items like tools on the desk without overloading it.
If you are going to be making a product that is food or pharmaceutical grade, then GMP rules dictate that the bench should have some form of washable surface such as 304 or 316 stainless steel.
These machines are normally used for R&D and small batch production. The reason for this is that if the user did need to run it daily then they would be much better off investing in an RTP 9 for the same or less money.
This machine will last 10+ years with the manual’s recommended maintenance.
The first parts that will go out will be wear parts such as the Teflon on the bottom of the boot. After this, there are a number of bushings that support the top cam that will wear out of tolerance.
The tooling will also need to be changed. The life of this will depend on the product that is being pressed.
All of these parts can easily be replaced.
No, the motor has a fan built into it to keep air moving over it. It also has a large compartment for proper ventilation. Finally, the perspex case does not retain enough heat to create an issue.
Yes, but it is not as easy. There is a handle mounted on the bottom of the motor that allows you to tune the press.
There is also a jog function on the press that allows you to rotate the machine slowly. This can also be used to change tooling and tune the press. It is important to remember that if using the jog function the doors will still have to be closed. Also, if the machine jams, the operator should release this button immediately.
Yes and no. The motors on the DTP 12 and 25 are both larger than the motors on the TDP 1.5. They are both flange mounted directly onto a gearbox which is then directly mounted onto the end of the top cam to drive the press.
Yes. The DTP 12 and DTP 25 come with anti-vibration feet. You can always check if the bench that the machine is mounted to is sturdy or place the machine on a rubber or foam mat to reduce any noise caused by the vibrations.
The DTP 12 and DTP 25 are not traditionally very loud machines so this should not be necessary. If your machine is making excessive noise or vibrations, then please reach out to LFA for support.
Yes. The perspex case is held in place with 4 screws and can be removed for cleaning or easier access to work on the machine.
All of the contact parts can be found in the IQ/OQ documents here:
They are 304 SS, GCr15 (or S7/D2 depending on tooling) and Acrylic.
No, sorry this machine is a gravity feed tablet press. Because of its design, we are not able to fit a force feeder to it. If the customer requires a press with a force feeder attachment, then they will have to look at rotary tablet presses.
If you are pressing a food grade product then we would recommend a combination of H1 And H2 greases. This will depend on your company's own internal practices. We also have a lubrication schedule that tells you the recommended viscosities and how often to apply the lubrication. This can be found here: DTP 25 Lubrication Schedule
On the DTP 25, there is no visual indicator for the fill depth.
You can see where the upper punch is set, giving you an estimate of the tablet thickness. However, because the tablet thickness is also dependent on the position of the lower drift pin assembly and the lower punch, the machine can not give you an exact tablet thickness measurement.
The motor will be warm to the touch after 30 mins of running, but not hot. The exact temperature will depend on how much strain the motor is under. Using a higher punch pressure increases the strain on the motor.
However, the motor does have a fan fitted to it for cooling.
Yes, it has a grub nut to hold it in place and can be removed from the end of the motor. This allows you to get a stronger grip onto the press with a tool. LFA does not provide additional tools.
On the old DTP 12/25, the manual rotation wheel is located on the bottom of the motor. This can make it difficult to grip.
To make it easier for the operator to use the handle in the event of a jam, you can remove the perspex between the motor and the pressing section. If you require more space than this, then the doors and back cover can be removed as well.
No, it will not need to be replaced every time. To avoid cross contamination between two different products, it should be removed and cleaned between batches.
The wearpart should also be changed once it has become worn down. This part is designed to protect your tooling, die plate, and boot from excessive wear. It should be replaced once the fitting screws become flush with the face of the plastic.
You might also want to change it in the event that it collides with a lower punch. This can only happen if the press is calibrated in a way that exposes the lower punch such as overadjusting the ejection height. If this happens, then the seal might leak powder and need to be changed.
The DTP can be set up to run on 110v for the USA and 240v for the UK and Europe. The main motor on the machine consumes 1.5 kW for the DTP 25 and 1.1 kW for the DTP 12.
Please contact us if you are unsure about the power supply you have for the specifications of the machine.
No, the perspex should not condensate. Tablet presses work when pressing dry powders. With that said, there should be no moisture on the inside of the press to condensate onto the perspex.
On top of this, the perspex casing is not perfectly sealed, so it will not retain any humidity in the press, making it hard for condensation to form.
The DTP 25 does not come with a vacuum attachment by default. It would be possible to fit one, but this is not something that LFA currently offers.
They are both able to press tablets that are as small as each other, since tablet sizes are determined by the diameter of the tooling. LFA is able to make tooling as small as 1mm in diameter, but it is extremely expensive and prone to breaking.
The DTP 12 or 25 will come with a plug wired to run on your local power supply. If you think that you might require something special then please do get in contact with the sales team.
On the side of the press, there is a powder isolator switch. This has the ability to be locked with a small lock.
There is an emergency stop button and a power isolator switch on the machines.
This depends on your product. If your product is very fine and free flowing, then you will get a higher percentage of loss than if your product is granular. Most products on a DTP 25 will have a loss rate of about 1-5%. If it is higher than this, then it would be worth speaking with our team about how to best reduce it.
At the moment we ship to all countries except the following countries because of embargoes:
Syria
Yes, each of the feet is on threaded studs adjustable. We would recommend however that you also ensure that the work surface that you put the DTP 25 on is also level.
No, it will not. It has two sensors that will shut the machine off in the event that the doors are opened.
Some of the older machines are not fitted with this function, however we are able to fit them as an aftermarket addition.
Yes, the tooling is changed in the same way as all TDP tooling. The top punch is held in place with a locking nut, the die is held in place with 2 set screws, and the lower punch is held in place with a grub nut.
The one way in which it varies from the TDP range is that the baseplate is not able to be removed. This means if the centre die gets stuck in place, you will need to lower the ejection height and lift lift up the die by hand.
The warranty on the DTP 25 is 1 year from the date that it is shipped to you. Contact us if you need to make a warranty claim for a replacement part. Please make sure that you have your DTP 25’s serial number on hand as we will need it to submit your claim.
The only parts that are not included under the warranty is the tooling. The fair usage policy more details about our warranty can be found here: Warranty
Yes, there are a number of methods to automatically fill the hopper of a tablet press these are:
Corkscrew / Archimedes screw - In this method, you fill a large hopper and the powder is lifted up into the tablet press using the screw. Most of these machines have an adjustable speed so that you set the speed to match the tablet press.
Drop through - This is where you mount the mixer on a stand over the top of the press. Once the mix has finished, you open the valve on the mixer and all of the powder falls into the press. This method has a number of disadvantages such as construction, cleaning, and height requirements.
Inline Vacuum Pump - This method sucks the powders out of the bin and lifts them up into the hopper. It is often controlled by attaching a sensor to the hopper so that it knows when it is full and when it needs to pump.
While all of these methods are available LFA does not sell them.
It is also important to remember that we recommend having someone with the press at all times so that in the event of an emergency or a jam they are able to shut off the press.
Finally, with the DTP 25 it is considered an R&D or small batch machine, so we would not recommend using it for large batches. Normally, an automatic feeder would be used to run a large tablet press or capsule filler for extended periods of time.
No. We do not currently offer an option to have the tablets come all the way out of the press and go directly into a tablet de-duster.
This is because the DTP 25 is not designed to do large runs of tablets. If you plan on producing more than around 1,000 tablets at a time, we highly recommend the RTP 9 Rotary Tablet Press.
No. The DTP 25 does not currently come fitted with load cells to show the pressure being exerted in compression or ejection.
Yes, the DTP 25 takes Universal TDP tooling from LFA and is able to make a tablet with a maximum diameter tablet of 25mm.
Yes, we have a full manual for the DTP 25. This can be found here:DTP 25 Manual
This includes instructions on how to use the control panel.
At LFA we currently offer IQ (Installation Qualification) and OQ (Operation Qualification) documents for all of our machines. We do not currently offer PQ (Performance Qualification) documents for machines. If you require them, then you will need an internal team to set up all of your own SOP’s. In the event that you have this person/team then they will be able to create your PQ documents.
There is no difference in the tooling for the DTP 12 and DTP 25. They both take TDP Universal Tooling. More details on TDP Universal tooling can be found here: TDP Tooling
No. At LFA we do not offer customization on any of our machines other than tooling. This allows us to support you with the parts that we keep in stock.
Yes, you can change the tooling on the press. It is important that you are able to do this. It is not a hard process and can be done in under 30 mins.
That will depend on how often you use it. We would recommend cleaning it at the end of every run, and in between products where it is important to ensure no cross-contamination.
Yes. You need to keep the press within the working range of 10-40 degrees c and a relative humidity of around 70%.
If the temperature or humidity gets too high, not only will it affect the mechanics of the press but it will also likely cause issues with your powders.
At the moment we only offer the documentation for this machine in English. However, if you require documentation in another language, we would be happy to work with you to get them translated. Please get in contact with our team for more information.
You are not able to check the operational status or tablet information through the control panel. This only displays the speed of the machine and in the event of a jam, an error code if the emergency stop button is applied.
No, there are a number of parts that are not the same on the two presses.
It takes around one full day. In this time you should be able to cover tooling changes, cleaning, and maintenance.
We can provide this training for free in one of our showrooms after you purchase a press.
No, sorry the warranty is for parts only. If you need your machine serviced and you do not feel confident to do this, then we would be happy to do so. This is, however, a charge for service. More information on this can be found here:
As with all machines, the DTP 25 will have parts on it that over time will need to be changed or that can become damaged through user error. Below is a list of parts that LFA has come to recognise as the most frequently damaged or that have been designed to wear so that more expensive parts of the press are protected.
Tooling - The tooling on the DTP 25 can become chipped or broken. Lead times for a new set of tooling can take as long as 6-8 weeks, so we recommend having a spare set or two. This is especially true if the tooling is customised.
Here is a link to the tooling page where it can be purchased:
Boot - The DTP 25 boot is formed from a brass casting. This part can become trapped between the die bore and the upper punch and usually happens from user error when the upper punch has not been secured correctly. While we hold this part in stock at all of our locations it can reduce waiting to have a spare.
Here is a link to the page where the TDP DTP 25 boot can be purchased:
Boot DTP 25 | Machine Spare Parts | Replacement
Boot Teflon Pads - On the bottom of the boot on the DTP 12/25 there are 3 pads that are used to protect the tooling and the boot against the die table. These pads are made from Teflon and are designed over time to wear to avoid damage to more expensive parts. You will get one free set of these wear parts when you buy the press but it can be a good idea to have another set in stock.
Here is a link to the page where it can be purchased:
Boot Teflon Pads DTP 25 | Machine Spare Parts | Replacement
Upper Cam Bushing - The upper cam bushing is a brass wear part that is used to keep the upper cam from coming into direct contact with the base of the machine. This part will need to be replaced after around 500 - 1,000 hours depending on the product being pressed and the pressure being used.
Here is a link to the page where the upper cam bushing for the DTP 25 can be purchased:Upper Cam Bushing DTP 25 | Machine Spare Parts | Replacement
Fill out your details and our team will provide you with a full quote as soon as possible.