Microcrystalline Cellulose
- Excellent Binding Agent
- Tasteless and Odorless
- Plant Extract
Connect with Our Team
If you have a question, require bulk pricing or would like more details about Microcrystalline Cellulose, please complete the form below and someone from our team will be in touch with you soon.
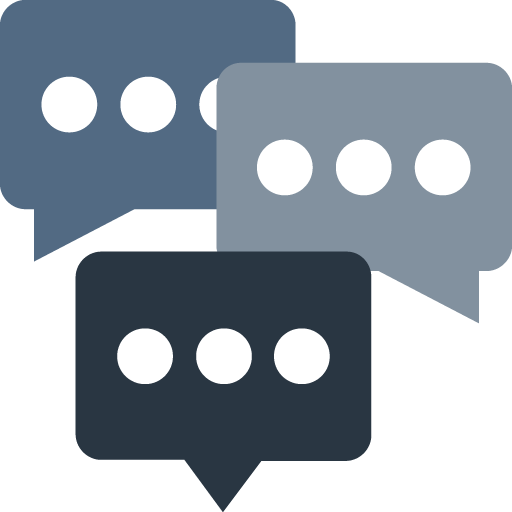
What exactly is the ideal excipient? The one which helps make ingestion easier for customers and manufacturing simpler for producers. Not just an excipient which is permissible to use, but one that stretches beyond standard functionality. Microcrystalline cellulose may be the exact binding agent you are searching for. It won't gel like methyl-cellulose and if compared to other binding agents it appears to provide the optimal degree of brittleness whilst staying lubricant sensitive.
Main Benefits
The main benefits of Microcrystalline Cellulose are:
- Higher compressibility
- Increased flow
- Strong binder
- Odorless, tasteless
- Non-reactive
- Low-absorption
Which Grade is Best for You?
LFA Machines is able to offer you 5 different grades of Microcrystalline Cellulose. The grade names are 101, 102, 200, 301, and 302. You may be most familiar with our Microcrystalline Cellulose 102 grade which we can offer to you at 1kg, 2kg, 5kg, 10kg, and 20kg bags.
Some noticeable differences between the grades are the following:
- Microcrystalline Cellulose 101 has the finest of particles, with a bulk density of 0.296g/cm3 . It is most suitable for wet granulation with excellent direct compression
- Microcrystalline Cellulose 102 has an average particle size with a bulk density of 0.308g/cm3 and is the most common grade of Microcrystalline Cellulose used to its high compressibility.
- Microcrystalline Cellulose 200 has a larger than average particle size, with its bulk density being 0.282g/cm3. Grade 200 has superior flowing properties and is commonly used to correct API flow deficiencies.
- Microcrystalline Cellulose 301 is very similar to Microcrystalline Cellulose 101, but has a larger bulk density of 0.358g/cm3
- Microcrystalline Cellulose 302 is very similar to Microcrystalline Cellulose 102, but has a larger bulk density of 0.359g/cm 3
Microcrystalline Cellulose, generally named MCC, is produced in a controlled environment. The end result is a pure, white powder without any taste or smell, able to add form and hardness to your tablets. MCC maintains the necessary advantages of a diluent. It is effective as a bulking agent in your tablet or capsule, giving the desirable weight for your customers. Microcrystalline cellulose has minimal bulk density, increasing flow characteristics. Easy flow helps to ensure that each ingredient is consistently spread throughout a mixture. If the mix is consistent, each tablet will have the same quantity of each ingredient at the end of production, creating a quality product.
Microcrystalline Cellulose really does its job, and also it does it well. It works well with many other popular excipients and is a integral part of many manufacturers formulas. Binders undoubtedly are a crucial element in the tableting process simply because they ensure “hardness” in a tablet. Additionally, compressibility affects all aspects of the final product, for example, disintegration, dissolution and absorption. MCC is directly compressible and therefore can be compressed into a tablet without having to granulate or process a mix, making the overall manufacturing process more efficient.
Compressibility and binding are both unquestionable characteristics of Microcrystalline Cellulose. Neither of these characteristics deter its ability to dissolve with ease once in tablet form, a crucial element of any tablet or capsule. MCC is safe to consume in normal amounts, and broadly used as an excipient for tableting. Additionally it is a natural source of dietary fiber and is also non-caloric. Above all else, MCC is inert, meaning it will not react to or interfere with other substances.
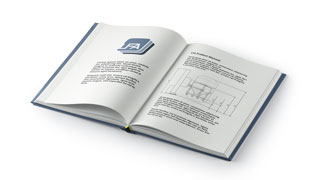
Get Information on
Microcrystalline Cellulose
Enter your details to get the User manual, Spec Sheet and Video links for Microcrystalline Cellulose
Overall, this product could possibly be what you are searching for. It is sought-after since it is amongst the top diluents with outstanding binding qualities, and will also preserve these properties for you. Your process of formation will become easier as a result of this ingredient. With its advantages and uses, Microcrystalline Cellulose is your ideal choice for a binding agent. Using MCC alongside other excipients makes production run smoothly and efficiently.
Name | MCC 101 | MCC 102 | MCC 200 | MCC 301 | MCC 302 |
---|---|---|---|---|---|
CAS number | 9004-34-6 | ||||
Molecular formula | (C6H10O5)n | ||||
Appearance | Fine white powder | ||||
Physical state | Solid | ||||
Storage | Store at room temperature | ||||
Melting point | 260–270 °C; 500–518 °F | ||||
Bulk Density | 0.296g/cm3 | 0.308g/cm3 | 0.282g/cm3 | 0.358g/cm3 | 0.359g/cm3 |
Tapped Density | 0.453g/cm3 | 0.455 g/cm3 | 0.454 g/cm3 | 0.452g/cm3 | 0.453g/cm3 |
Solubility in water | None | ||||
Documents |
Intolerance Data Technical Specification |
Yes, it does not matter what age, size or sex the person consuming the products is. It is, however, important to check the intolerance data.
Yes, all of the excipients are safe for human or animal consumption. There are some precautions that should be taken when handling them and there are some people that might have intolerances to some of them. Information on this can be found in the products MSDS and Intolerance Data Sheet. This can be found in this section for every excipient.
Yes, there are all of them can be found in the intolerance sheets for each product. The intolerance sheets can be found here: https://www.lfatabletpresses.com/product-data
Yes, all of our Excipients are extracted from natural sources. For more information please visit the individual product pages.
Yes. CoA stands for Certificate of Analysis this is also known some times as an MSDS (Material Safety Data Sheet) all of the information contained in a CoA is inside the MSDS for every LFA product which is emailed to you after purchase.
It is unlikely that you will be able to produce tablets without using any Excipients at all. Certain products do bind without Excipients, but then do not flow through the machine. We advise that you use our Firmapress ready mix as this works with 99% of products.
Yes. There are two things at play here. You can get hygroscopic and hydrophobic excipients. Hygroscopic means that they take on water quickly, while hydrophobic means that they repel water.
There are products know as supper disintegrants. These products help the breakdown of tablets. At the moment LFA does not sell any supper disintegrants.
Magnesium stearate is hydrophobic this means that it will slow the breakdown of a tablet.
However, it is used in such small amounts that most of the time it will not make a difference to our customer's products. If they would like to be sure then they should conduct what is known as a disintegration test.
Firmapress - 2 years form batch date.
Dextrose - 3 years from batch date.
Dicalcium Phosphate - 3 years from batch date.
Microcrystalline Cellulose -
Magnesium stearate -
Lactose - 2 years from batch date.
Silica Dioxide - 2 years from batch date.
here are 6 steps that should be followed as a general rule of thumb when cleaning contact surfaces that have come into contact with powders:
Dry Clean - First you need to remove as much of the dry powder as possible. You can do this using a hover/vacuum. Make sure that the vacuum you are using has a filter good enough to handle fine dust.
Wet Clean - Next you need to perform a wet clean. This can be done with warm water and soap or if available an ultrasonic cleaner.
Rinse - Next you need to rinse off any soap with potable water (drinking water). You do not have to do this if you used an ultrasonic cleaner in the last step. It is important to ensure that all parts are thoroughly dried immediately after washing to avoid any rusting.
Sanitise - Next you need to sanitise the surface. This step is recommended by the FDA. There are a number of sanitising solutions available designed to be applied and left on.
Lubricate - You now need to lubricate any parts that require it. This should be with the appropriate grade oil or grease considering your use and greasing chart. Store - Finally store any of the parts in a cool dry place. If you are storing them on the machine then make sure the machine is in a temperature controlled environment with low humidity.
We offer Microcrystalline Cellulose, Magnesium Stearate, Dicalcium Phosphate and Firmapress in our range of excipients.
Microcrystalline Cellulose is a binding agent, which holds the content of the tablet together.
Dicalcium Phosphate is a flowing agent and helps move ingredients through the machine before they are compressed.
Magnesium Stearate is a dry lubricant and helps again with the movement of ingredients through the machine but also helps with the ejection of the tablets from the machine. Please note that Magnesium Sterate does not bind by itself.
Firmapress is an all in one mix of Microcrystalline Cellulose, Magnesium Stearate and Dicalcium Phosphate.
Dextrose - approx 100 mesh
Dicalcium Phosphate - approx 100 mesh
Microcrystoline Cellulose - approx 120-200
Magnesium sterate -
Lactose - 80 mesh
Silica Dioxide -
Firmapress - 100-200 mesh
Dextrose - Sweetener, binding agent, good for chewable tablets or candy.
Microcrystalline Cellulose - Binder, filling agent. Good at binding tablets and making them bigger. It can also be used as a filler for capsules.
Magnesium stearate - Dry Lubricant. This stops products from getting stuck to the tooling. It can also help with powder flow issues and caking issues.
Lactose - Binder, sweetener and bulking agent. It has a large mesh so it flows well but most people do not like it because of the intolerance issues.
Silica Dioxide - Flowing agent. This assist powders in flowing smoothly through the machines. It also helps with cacking issues where powders get stuck to the machine.
Firmapress - 2 years form batch date.
Dextrose - 3 years from batch date.
Dicalcium Phosphate - 3 years from batch date.
Microcrystalline Cellulose -
Magnesium stearate -
Lactose - 2 years from batch date.
Silica Dioxide - 2 years from batch date.
If your product does not bind well then we would recommend using MCC. This can be used in any % the limiting factor is the size of the tablet.
If the amount of MCC you would have to use would be too much or if you do not want to use MCC then you have 3 other options: Ask your supplier for a directly compressible or tabletable grade of your product. Spray dry your product. Wet granulate your product.
If your product is sticky then you will need to add a dry lubricant to your mix. For this, we recommend magnesium stearate.
We do not recommend that you add more than 1% to the mix as more than this can cause capping. If your product is still sticky at this point then we would recommend looking into granulation.
If your product or API is clumpy then you will need to add an anticaking agent. For this, we recommend silicon dioxide. We only recommend adding a maximum of 2% of this to the mix