RTP 33 Rotary Pellet Press
- 99,000 Pellets or Tablets per Hour
- RTP Specification Tooling
- 40kN Max Pressure
The RTP 33 is an exceptionally powerful, continuous automatic rotary pellet press designed for pharmaceutical, chemical or food technology manufacturers who need to produce pellets in industrial quantities. The 2.2 kW, three-phase motor of this pellet press drives 33 sets of dies, pressing granular or dry powdered raw materials into round pellets of up to 12 mm in diameter. With a maximum pellet producing capacity of up to 99,000 units per hour, the RTP 33 can be relied on to satisfy large-scale commercial demand for high quality pellets of a standardised weight.
Connect with Our Team
If you have a question or would like more details on the RTP 33 Rotary Pellet Press, please complete the form below and someone from our team will be in touch with you soon.
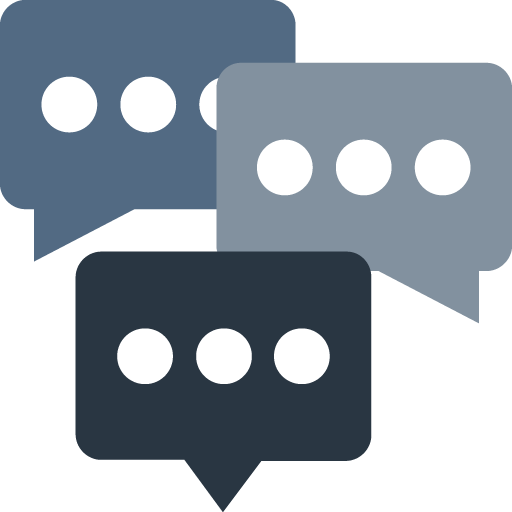
Despite its power and large productive potential, the RTP 33 is an extremely economical choice that produces pellets at a low cost-per-unit. It is especially efficient in its use of raw materials, thanks to an integral powder suction unit that avoids wastage. The machine has been built from industrial grade components that will ensure a long working life, and it is very simple to operate, with minimal controls to learn. Thoughtful design also ensures that this pill press is easy to maintain.
Aimed squarely at large-scale mass production, the RTP 33 is one of the fastest pellet pressing machines in our range, and a natural choice for commercial producers.
Main benefits of the RTP 33 Pellet Press
- 33 cutting heads, giving mass production speed of up to 99,000 units per hour
- Powerful 2.2 kW motor
- Highly efficient - built-in powder suction unit recycles powder, avoiding wastage and keeping dies free from obstruction
- Built-in hydraulic power pack
- Mechanical buffer unit to prevent overload damage to punches
- Simple to operate through electric control system
- Easily adjusted turret speed
- 12 mm maximum pellet diameter
- Easily adjusted pellet thickness up to maximum 6 mm thick
- 40 kN maximum pressure for durable, properly compacted, pharmaceutical grade pellets
- Easily removable parts for fast servicing and minimal downtime
- Highly reliable with rugged, industrial quality construction
- A solidly engineered pellet press for years of uncomplicated commercial use
Features
Suitable for pressing granular material or dry powders, the RTP 33 rotary pellet press benefits from an impressive set of features. It is built on a double-press format, with 33 cutting heads giving a manufacturing capacity of between 43,000 and 99,000 units per hour depending on the type of raw materials being used. A reliable 2.2 kW motor generates large reserves of power that are managed via simple electronic controls. The motor is complemented by refinements such as the built-in hydraulic power pack, and a mechanical buffer unit to prevent overload damage to the punches of the pellet press.
Given that this is a machine intended for large-scale manufacturing, and which processes a substantial quantity of raw materials, it is essential that it uses those raw materials efficiently. The RTP 33 pellet press achieves this brilliantly, thanks to its built-in powder suction unit that prevents wastage by automatically recovering excess powder from the die area and recycling it. This also keeps the die heads clear of obstruction, and helps ensure smooth operation without delays.
All the relevant settings on this pellet press are easy to adjust, including turret speed, fill depth, diameter and pellet density. Up to 40 kN of available pressure means that the RTP 33 produces consistently solid pellets with a professional finish. A maximum fill depth of 15 mm gives a maximum pellet depth of 6 mm, making it suitable for a wide range of applications. The RTP 33 produces round pellets up to 12 mm in diameter, and the dies can impress designs or letters onto the pellet surface.
RTP 33 Pellet Press in Use
The outstanding impression when using this pellet press is one of speed and efficiency. The 33 dies turn out pellets at an eye-blurring rate, and the powerful motor sounds reassuringly calm.
The speed selector offers two choices, depending on the type of pellet you are pressing. Slow speed gives a pressing rate of between 43,000 and 79,000 pellets an hour, and is intended for difficult-to-press materials such as ceramics. High speed gives a pressing capacity of 59,000 to 118,000 pellets per hour, and is suitable for normal raw materials.
When it comes to changing the dies, despite the sheer number involved, the process itself is straightforward and easy to master.
Because this pellet press is intended for long runs that produce industrial quantities, it has two large hoppers for raw materials so that the operator does not spend their time constantly running backwards and forwards to fill the machine. Maintenance is also carefully thought through, with easy access to internal parts which can be lifted out for replacement or repair.

Download The RTP 33 Manual & Specification Sheet For Free
This information will help you figure out what the RTP 33 can do for your business.
Technical Specifications
The RTP 33 pellet press measures 1100 mm x 480 mm x 680 mm, and weighs 1,000 kg. Inside the crate, the dimensions are 1600 mm x 950 mm x 960 mm. It produces a maximum pressure of 40 kN and has a turret speed of 30 r/min. Its motor operates at a maximum power of 2.2 kW. Available for three-phase compatibility, the machine can be supplied with 220v use.
The maximum fill depth is 15 mm, and the maximum diameter for round pellets is 12 mm. The machine produces pellets up to 6 mm thick.
Our View
This is a remarkably efficient machine that gets on reliably with the job of churning out top-quality pellets at a consistent rate. The RTP 33 is a very good value, considering the speed and build quality it offers. Weighing in at 850 kg it is a sturdy piece of equipment that has been built with solid practicality in mind rather than good looks, but that only adds to its appeal. If you are a chemical company, raw material technology company, or any manufacturer needing large-scale production of round pellets at a low unit cost, this pellet press will meet your needs admirably.
Specification | Value |
---|---|
Product | RTP 33 |
Tooling Specification | RTP Tooling |
Number of dies | 33 |
Max Pressure (kN) | 40 |
Max Diameter of Tablet | 12 mm / 0.47 in |
Max Fill Depth | 15 mm / 0.59 in |
Max Thickness of Tablet | 6 mm / 0.236 in |
Turret Speed (r/min) | 14 – 30 |
Max Production Capacity Per Hour | 99,000 |
Number of Filling Stations | 2 |
Double Layered Tablet | Yes on request. |
Power US | 220 v, 3 phase, 2.2 kW, 60 Hz |
Power UK | 480 v, 3 phase, 2.2 kW, 50 Hz |
AMP's | 32 |
Height | 1600 mm / 62.99 in |
Width | 950 mm / 37.4 in |
Depth | 960 mm / 37.79 in |
Floor Loading (Static) | 9 kN/m2 |
Double Layered Tablet | Yes, on request |
Gross Weight | 1,150 kg |
Net Weight | 1000kg |
The tooling that fits the RTP 33 can also be used in the RTP 9 and RTP 41. The spare parts on the RTP 33 are not interchangeable with the other RTP models.
Yes and no. There are products that are more difficult to compress into tablets than others. As a result, these might require excipients to help the product bind into a tablet. If you have a formula which requires more force than 40 kN, and you are not able to increase the amount of binding agent, then the RTP 33 is not the right machine for you. If you are able to increase the amount of binding agent and decrease the amount of active ingredient, then the RTP 33 will work for your needs.
Yes, you can, but there are a number of requirements that we need to fulfill first.
You will need to contact our team and provide them with a copy of all of your MSDSs for all of the components of your mix.
We need to have a good understanding of your business and the challenges you are facing.
You will also need to book an appointment with the office that you would like to visit.
For more information please get in contact with the team: https://www.lfatabletpresses.com/contact
This is possible only if the weight of your tablets do not need to be the same in each shape and if your formula has excellent direct compression. Essentially, if you are able to press a tablet using the largest of the tooling sets, then the rest of them should work as well.
Yes. Very easily.
We have free lifetime technical support for all machines sold by LFA.
Just contact us with your machine serial number and we would be happy to help you with any problems.
If you require a lower maximum fill depth to help prevent waste, then yes this is possible, but you will need to reach out to your regional LFA office to order the necessary parts. However, we are not able to increase the maximum fill depth on the RTP 33.
Yes. You can order custom tooling here
Yes, you can put different formulations in each hopper as long as they have similar flow properties and would not react with one another. This would typically only be done when producing a dual layered tablet which would require some modifications to the machine for this to be possible.
It would be possible to use different formulations in each hopper without making a dual layered tablet as long as there was no issue with cross contamination because that certainly would occur to some extent.
Yes, the RTP33 can be run using only one hopper. However, you will be cutting the production capacity of your machine in half so there likely is no reason you should do so. It would be a better idea to simply slow down the turret to decrease the rate of production.
The standard RTP 33 does not come with a turret that fits Euro (ISO 18084) or TSM tooling. The turret and cams would need to be changed in order to accommodate this. You would be better off purchasing RTP tooling which is designed to fit the RTP 33.
Yes, the RTP 33 is capable of making dual layered tablets, however some modifications would be required to make this possible. It is recommended that you either order your machine with the dual layered tablet capability or return your machine to LFA so that our technicians can make sure that the change is completed properly. That being said, if you have an experienced technician on hand the parts are available to purchase in a set.
Yes, the RTP 33 will be able to function properly with corrosive materials. However, specialized tooling would need to be used to help prevent wear and to extend the life of the machine. The machine would also need to be thoroughly cleaned and lubricated every time it is used. Any corrosive material used with a machine will cause excessive wear to the wear parts. As a result, it is likely that they will need to be replaced more often.
Unless you have a formula with excellent direct compression and flow properties you should never run the RTP 33 at its maximum speed. On any rotary press, as you increase the speed of the turret’s rotation, you are also decreasing the dwell time. This refers to the amount of time that the tablet is under compression. As dwell time decreases, so does the compression force, so increasing the speed on a rotary press actually decreases the amount of pressure that machine is using. Even at the highest pressure setting, this will still be true as you increase the speed of the turret's rotation. For this reason it is not recommended to run the machine at its highest rate of production.
Yes, it will be very important for the operator to have a thorough knowledge of the cleaning and maintenance processes for the RTP 33. Cleaning should be done after each day the machine is in operation or in between batches where cross contamination could be an issue. Maintenance should be performed regularly, as stated in the lubrication schedule. Both the cleaning and lubrication schedules can be found here:
Yes, the TDP and RTP range all have a weight adjustment for it.
on the TDP it is the bottom of the two cogs on the lower drift pin assembly.
Here is a link to a video showing you how to tune up the TDP 5: https://www.youtube.com/watch?v=4dTscUdRJzQ
Here is a link to a video showing you how to tune up the RTP 9 or the RTP 118: https://www.youtube.com/watch?v=YJFt5AFJ1hw
It is important to know that the exact weight of each tablet will vary from tablet to tablet.
A well-homogenized mix that has a consistent granule size should be able to achieve an accuracy of +/- 3% or less.
The RTP 33 comes with a keyed upper turret, however, if you are interested in purchasing a refurbished machine, it is always best to contact the relevant office to inquire if the machine does in fact come with one. If your product requires both the upper and lower turrets to be keyed, this will have to be done in our factory. The lead time for this will be about 8 weeks.
The RTP 33 does not have a force feeder option and is fed by what is known as a gravity fed system. A gravity fed system includes a specially designed hopper that feeds the powder into the feeder tray. The feeder trays are designed to allow the powders to drop into the die cavity when each station is positioned above the fill cam. The fill cam pulls the lower punch downward to allow for the die cavity to be completely filled prior to moving to the dosing cam. The dosing cam will then push out the excess powders and only the amount you have tuned your machine to will remain.
The RTP 33 does not have the ability to display a readout of the amount of pressure that the machine is tuned to. You could determine the amount of pressure being used by putting the finished tablets through a hardness test.
Yes, the speed of the RTP 33 is adjustable. This adjustment is done by manually turning a wheel on the front side of the press. The press also uses a clutch system which allows you to engage and disengage the turret rotation.
The RTP 33 comes with anti vibration feet which will help prevent the machine from moving around during operation while also reducing the vibration and overall noise. The weight of the machine alone is enough to keep the machine in place, though it is important to note that the machine will need to be installed on a level surface.
The speed of the RTP 33 will have some effect on the life of the tooling. However, this ultimately depends on how the tooling is maintained and the materials that you are compressing.
The RTP 33 is best suited for industrial production of fertilizer, chlorine, and ceramic tablets which would not be meant for human consumption. That being said, the RTP 33 is perfectly capable of producing tablets which are safe for human consumption. It would just depend on the regulations in the state or country you will be operating within.
The RTP 33 is a very durable machine due to its construction. As with all of the RTP rotary tablet presses, there are wear parts that are designed to be relatively easy to replace and to extend the lifetime of the machines.
The RTP 33 ships via FedEx freight in a wooden crate. The machine is bolted to a steel pallet inside. It is important to keep both the crate and pallet in the event that you need to have the machine sent back for repair or transport it to a new facility.
A basic cleaning will take around 1.5 to 3 hours, depending on how difficult the tablet formula is to clean. A thorough clean, which would include removing the turret, will take up to a working day. Unless you have experienced staff and the means of safely lifting the turret off of the machine, it is recommended that you send the machine back to LFA for this level of maintenance.
It is recommended that the RTP33 be cleaned and maintained as per the cleaning matrices and lubrication schedules found here:
Being that there are 33 stations and not 9 or 10 respectively, it will take a bit longer to fully clean the RTP 33. A basic clean down should take around an hour and a half for the RTP 33.
Only one operator is required to operate the RTP 33. It is LFA’s recommendation that the operator remain present while the machine operates.
This will depend on how well the RTP 33 is maintained over the course of its lifetime. With proper care, including the replacement of wear parts and tooling when needed, the machine should be able to produce 4.5 billion tablets. The tooling would need to be refurbished or replaced over time but it is certainly within the capabilities of the machine.
An experienced operator can change the tooling in the RTP 33 in 1-2 hours but it likely will take you around 3 until you have become comfortable with the process.
We've created a calculator on our website for most of our tablet presses. See the "profit calculator" tab on the product page and enter your profit per tablet to see how many running hours the press will pay for itself and how much profit per hour it will generate.
There are several differences between the RTP 33 and RTP 41. The RTP 41 comes with perspex doors which prevent contamination during production while also containing finer powders from entering the working environment. The RTP 33 does not have this feature. The RTP 41 also utilizes a Human Machine Interface, or HMI, to help monitor production and control the speed of the turret. The RTP 41 also has a higher maximum pressure of 80kn as compared to the 40kn of the RTP 33.
Yes, the RTP 33 can be fitted with a variable frequency drive, or VFD, which would allow you to run the press as slowly as needed.
The RTP 33 can be installed in an inexpensive cage which would make it more compliant in most instances. Unfortunately, there is not much more that can be done to make the RTP 33 more in compliance with regulations. You would be better off going with the RTP 9, RTP 10i, or RTP 41 if you are looking for a compliant rotary tablet press.
Unfortunately, the fill depth on the RTP 33 can not be increased to accommodate a larger tablet height.
Yes, the RTP 33 is capable of making dual layered tablets however there would be some modifications made and additional parts to make this possible.
The turret on the RTP 33 can be replaced in a day, though the change will require the use of a forklift or mechanical hoist system. We recommend that the machine be returned to your nearest LFA facility in order to properly replace the turret.
This will depend on your production capacity needs as the RTP 33 has a considerably higher rate of production. The reason for this is because it has 33 stations compared to 9 and the RTP 33 presses and fills on both sides of the turret and the RTP 9 does not. The RTP9 is suitable for the production of food grade products, however, so depending on the product you are making the RTP 9 may be the best option for your needs.
This will depend on the regulations in the state/province/country which the machine would be operated in. That being said, the RTP 33 would not qualify as a machine which would be suitable for most cleanroom environments.
Every LFA machine goes through a factory acceptance test or FAT both before it leaves the factory floor, and prior to being shipped to our customers. This is to ensure that any defects or issues can be dealt with prior to the machine arriving at your facility.
No, there are 3 specifications for Rotary Press Tooling and a number of different sizes that fall under them. These 3 specifications are RTP, Euro, and TSM. Under TSM and Euro tooling specifications, there are 4 common sizes: B, D, BB, and DB.
In order to determine whether or not your machine is still under warranty, you will need to call or email the office the machine was purchased from, and provide the serial number.
The RTP 33 allows the operator to adjust the speed, however, it does not come equipped with a variable frequency drive or VFD. This can be added to the machine, though this may add to the price and lead time.
Yes, the IQ/OQ documentation for the RTP 33 can be found on the website:
The manual and other documentation for the RTP 33 can be found here:
To ensure that you have the most recent version of the RTP 33 manual, you can always access and download it from our website. This can be found at the bottom of any page under “Product Data”, which is located under the Policies section.
The RTP 33 is no more difficult to tune and operate than the other RTP models. That being said, there is no Human Machine Interface or HMI as seen on the RTP 10i and RTP 41. The HMI allows users to monitor the fill depth and pressure settings on a tablet press, as well as the rate of production.
It depends on your location as every country has a different set of rules to define GMP compliance. We recommend checking your local regulations if you are unsure.
When you feel resistance on the adjustment knobs on the RTP 33, it is because you're attempting to make the adjustment while the tooling is under compression. You will need to make adjustments when the punches are not making contact with the roller cams.
Yes, the RTP 33 is perfectly capable of producing tablets as well as pellets. The reason that it is listed as a pellet press is because the machine is not suitable for most cleanroom environments.
The construction materials of the RTP 33 can not be changed. We recommend one of our other RTP rotary press models should this be required by your regulatory authorities.
RTP 33 vs RTP 9
The RTP 33 will utilize 33 tooling sets while the RTP 9 only has room for 9 so the production capacity will be far greater on the RTP 33. RTP 33 is able to fill and press and fill on both sides of the turret which also allows for a much higher production capacity. If you require more than 100,000 tablets a week you will be better off going with the RTP 33. The RTP 33 also has a larger footprint then the RTP 9 will have. Both the RTP 33 and RTP 9 lack the Human Machine Interface or touchscreen control as seen on our other rotary presses.
RTP 33 vs RTP 10i
There are many differences between the RTP 33 and the RTP 10i, the most obvious being the amount of tooling sets which can be fitted on each machine. The RTP 33 takes 33 tooling sets, while the RTP 10i can be fit with 10 tooling sets. Another difference is the materials used to build the machines. While the RTP 10i exterior is stainless steel, the RTP 33 is cast iron which has been coated in heavy duty enamel. This will make the RTP 33 unsuitable for certain applications. The RTP 10i also has a pre-pressure feature which helps to reduce ejection forces. This is helpful when when working with difficult formulations. The RTP 10i is also equipped with a force feeder, whereas the RTP 33 uses a gravity fed system. If your formulation does not have decent flow properties, it may be necessary to go with a machine which utilizes a forced feeder. The RTP 10i also has a higher maximum pressure (80kn) than that of the RTP 33 (40kn.)
RTP 33 vs RTP 41
The RTP 41 has 8 more stations than the RTP 33, so it will have a slightly higher production capacity. There is also a higher maximum pressure on the RTP 41 (80Kn) then that of the RTP 33 (40Kn.) The construction materials for the RTP 41 will also be in line with most GMP requirements, whereas the RTP 33 will not. The RTP 41 also has a slightly larger footprint than the RTP 33. Other than that, both machines will press tablets on both sides of the turret and can be modified to press dual layered tablets as a result.
As with all machines, the RTP 33 has parts that need to be changed over time or can become damaged through user error. Below is a list of parts that are most frequently damaged or have been designed to wear to protect more expensive parts of the press.
Tooling - The tooling on the RTP 33 can become chipped or broken. Lead times for a new set of tooling can take as long as 6-8 weeks, so we recommend having a spare set or two. This is especially true if you have custom tooling.
Here is a link to the tooling page where it can be purchased: Tablet Press Tooling
Fill Tray - On the RTP 33, there is a Fill Tray, or feed frame, that is used to spread the powder over the die table and into its cavity. It has been formed from cast brass with chrome plating. Because this part sits directly in contact with the turret and the die table, it has been designed to wear. This protects not only the die table, but also the tooling. If this part is damaged by a die that is sitting above the die table, for instance, then it is possible to refinish it using a flat stone, some oil, and 3000 grit sandpaper. When the “gates” underneath this part are so small that powder is unable to pass smoothly between them, then you will need to replace this part.
Here is a link to the page where it can be purchased: Fill Trays - RTP 33
Fill Tray Scraper Blade - The Fill Tray Scraper Blade, or take off blade, on an RTP 33 removes excess powder from the die table that has been forced out of the die cavity by the dosing cam. This part can become damaged if a die is protruding from the die table or if a lower punch jumps up from the dosing cam. In the event that this happens it will need to be replaced to reduce waste.
Here is a link to the page where it can be purchased: Fibre Fill Tray Scrapers - RTP 33
Ejection Cam - The ejection cam on the RTP 33 is designed to eject the tablets at the correct moment during the turret's cycle. This partcan not be tuned and is fixed in place. Over time, this part can wear. As this happens, the ejection point of the tablets will get lower until they are not ejecting correctly from the die boars. There are 3 main causes of this:
While it is possible to shim the ejection cam, the wear is often not consistent across the entire cam. This can lead to excessive pressure on the motor, timing belt, and bearings in the press. At this point, we would recommend swapping out the ejection cam.
Here is a link to the page where it can be purchased:Ejection Cam - RTP 33
Fill Cam - The fill cam on an RTP 33 pulls the lower punches down so the die cavity can be filled with powder. This part is built from brass and designed to wear so both your tooling and press are protected. As this part wears, the maximum fill of the lower tooling can become inconsistent and effect tablet weights. There are a few main ways that the fill cam can become worn:
If the fill cam is inspected and there are obvious signs of damage then it is best to replace it to avoid damaging your machine.
Here is a link to the page where the fill cam can be purchased: Fill Cam - RTP 33
Dosing Cam - The dosing cam on the RTP 33 is used to calibrate the press to produce the desired tablet weight. This is done by pushing excess powder out of the die boar after it has been filled. If this is worn, then the tablets could become inconsistent causing the machine to no longer conform to mix recipes. There are a few main ways that the fill cam can become worn:
If you think that you have an excessively worn fill cam, you should inspect it for gashes or other damage. If it does not have a smooth and consistent incline, it should be replaced immediately.
Here is a link to the page where the fill cam can be purchased: Dosing Cam - RTP 33
Upper/Lower - Main Pressure Rollers - The Upper and Lower Main Pressure Rollers on the RTP 33 apply all of the pressure to the tooling. If these become worn, they can damage the tops of your tooling causing tablet hardness inconsistencies. This is typically caused by general wear and in some cases, excess punch pressure being applied. You should visually inspect your cams for signs of wear and replace them.
Here is a link to the page where the fill cam can be purchased: Upper Rolling Cam - RTP 33
LFA recommends that you use some variation of mechanical lifting system in order to safely move the machine. Whether that be a forklift, hoist, or pallet jack doesn’t matter, but the machine is simply too heavy to move without doing so. There is an eye bolt conveniently located on the top of the machine which can be used with a hoist system.
The only differences between a tablet press and a pellet press will have to do with the materials it is composed of and the safety measures found on the machine.
A tablet press will usually be made with stainless steel and other food grade contact parts while also including an enclosure. This enclosure prevents contaminants from getting into the working area and powders from becoming airborne in the lab or manufacturing facility.
A pellet press will utilize the same mechanics but may not have all food grade contact parts. The RTP 33 does for the most part, with the exception of enclosures.
The lifetime of tooling is difficult thing to calculate. This is because it is dependent on a number of different factors.
The first thing to consider is the product that is being pressed. The softer the product, the less of a sandpaper effect it will have on the tooling. If the product is very coarse, however, then the likelihood of wear increases as it moves over the face of the upper and lower punches during compression.
The next thing that affects the life of the tooling is its shape. If the cup of the tooling is very deep, then the powder will have to move a lot further over its surface during compression. As a result, this causes more wear and shortens the life of the tooling.
The surface of the punch will also determine how long the tooling lasts. For coated tooling, the material used to coat the punches will influence the tooling's longevity. For uncoated tooling, the type of steel should be considered in relation to the tooling’s lifetime.
Ultimately, it is impossible to give an exact figure without running the tooling in a production environment.
A good rule of thumb is this:
The standard life of shelf tooling from LFA should make 2-5 million tablets.
Standard S7 tooling that has been customized will make around 10m tablets.
A well designed set of customized tooling that has been coated can make up to 65m tablets.
These estimates are applicable for tooling that has been cleaned properly and used correctly in the press.
The RTP 33 is capable of producing a maximum diameter of 12 mm when pressing a round tablet, while 14 mm is the longest dimension for non-round tooling. This is due to the dimensions of the tooling that fit the RTP 33 turret.
The RTP 33 is composed of HT200 and HT250 cast iron. The spare parts are be made from materials which best suit their purpose.
For instance, the fill or feed tray is made from brass to prevent damage to your tooling should the tray or tooling not be installed properly and make contact.
The scraper blade, which is located on the left hand side of the fill tray, is made from composite materials. This prevents it from damaging the turret while it clears it of fine powder.
The take-off blade, which is on the opposite side of the tray, is made from stainless steel as it makes contact with the product.
The hoppers are also composed of stainless steel.
The operator(s) should be wearing appropriate PPE that is suitable for the product being used with the machine. At no time should an operator have their hands near the working area while the machine is operating. All loose jewelry should be removed. Hair should be pulled back and covered.
In order to prevent cross contamination between batches of different products, the machine should be thoroughly cleaned. All tooling should be removed, cleaned, and coated in a light food grade oil. The machine should be cleaned from top to bottom, paying particular attention to the turret itself. Using a tool such as a die seat cleaner will ensure that the cavities that the dies are installed into are properly cleaned. LFA is happy to provide you with a set, which can be found here:
As with any tablet press, it is good to have a particle size of around 80-60 mesh.
This would be large enough to avoid large losses and small enough to flow well through the machine. If the powder is finer than this then you are going to experience a larger level of loss.
If the particles are larger than this then it might not flow through the machine well and get caught as it is trying to enter into the die bore.
This being said every powder is very different and you will need to do tries to work out what is best for them.
The only parts on the RTP 33 that are not covered under warranty are the tooling sets. If you receive tooling that is not exactly to the specifications defined in the tooling drawings, then we will offer a refund or have them remade. The warranty is valid for 12 months, the complete terms and conditions can be found here:
We send out all machines with the local plug on and set up to run on the local power supply.
The main reason one would choose the RTP 33 rather than the RTP 41 would be the price difference. If your product does not need to be safe for human consumption, then it would make sense to go with the RTP 33. The RTP 33 is rugged, sturdy, and will be able to produce tablets/pellets at a high rate of production.
Get a capsule filler.
You will not be able to make tablets.
Click here for more information https://www.lfacapsulefillers.com/
There are a number of ways we are able to support you:
- Every machine comes with a full manual that is emailed to you after purchase.
- There is a large range of video tutorials to teach you how to use the press.
- The machine comes with lifetime technical support. You can call, Skype or email to get answers to your questions and problems.
- We also offer free training at any one of our regional offices.
If after all of this you are still struggling to use your press, we are able to come to you. This is a service we charge for.
More information on this can be found here: https://www.lfatabletpresses.com/services
The RTP 33 can be fitted with RTP tooling which is slightly different from TSM or Euro standard tooling. A drawing which represents the dimensions can be found here: Product Data
There are no special requirements when shipping tablet presses or capsule filling machines over state lines. The due diligence process, however, will be necessary in order to ship these machines anywhere within the United States.
If your product needs to be manufactured in a GMP rated facility, you would want to go with the RTP 10i or RTP 41 instead. The RTP 33 is not jacketed in stainless steel and does not have the perspex doors for preventing contaminants from entering the working area and fine powders from making their way into your facility.
The RTP 33 is manufactured at our production facility in Taiwan.
Depending on the pressure settings on the machine, the upper and lower roller cams may not actually spin while the machine is under operation. They are capable of spinning so as to more evenly distribute the wear to the parts, however, they will not always spin.
The reason that the RTP 33 is only capable of producing a 12 mm maximum diameter tablet has to do with the tooling and not the machine itself. The tooling which fits the RTP 33 turret cannot produce a tablet larger than 12 mm in diameter because there is not enough room in the dies for this to be possible. The turret and cams can be swapped out to fit larger dimension tooling such as Euro D; however, after the cost and time it would take to make the switch, you would be better off going with the RTP 10i or the RTP 26.
The RTP 33 uses two hoppers and two feed trays because the machine is set up to fill and press on both sides of the turret. As a result, 66 tablets are produced each time the turret makes a full rotation . This also allows for dual layered tablets after making some modifications to the machine.
You will always need to adjust the fill depth and pressure settings on the RTP 33 when using different sized/shaped tooling sets. The speed can remain constant between different sets of tooling as long as the pressure and fill depth settings are adjusted accordingly. It is important to keep in mind that whenever you are increasing the speed of a rotary press you are decreasing the dwell time or time in which the powders are under compression and therefore decreasing the pressure.
The speed at which a press can be run will vary depending on the raw materials in the mix that is being pressed. If the mix has a less than ideal flow rate, then the speed of rotation would need to be slowed to down to ensure a complete fill during each rotation. Additionally, if your mix has poor direct compression, the dwell time must be increased as much as possible to make up for this.
Unless you have a formula with excellent direct compression and flow properties you should never run the RTP 33 at its maximum speed. On any rotary press, as you increase the speed of the turret’s rotation, you are also decreasing the dwell time. This refers to the amount of time that the tablet is under compression. As dwell time decreases, so does the compression force, so increasing the speed on a rotary press actually decreases the amount of pressure that machine is using. Even at the highest pressure setting, this will still be true as you increase the speed of the turret's rotation. For this reason it is not recommended to run the machine at its highest rate of production.